New material research
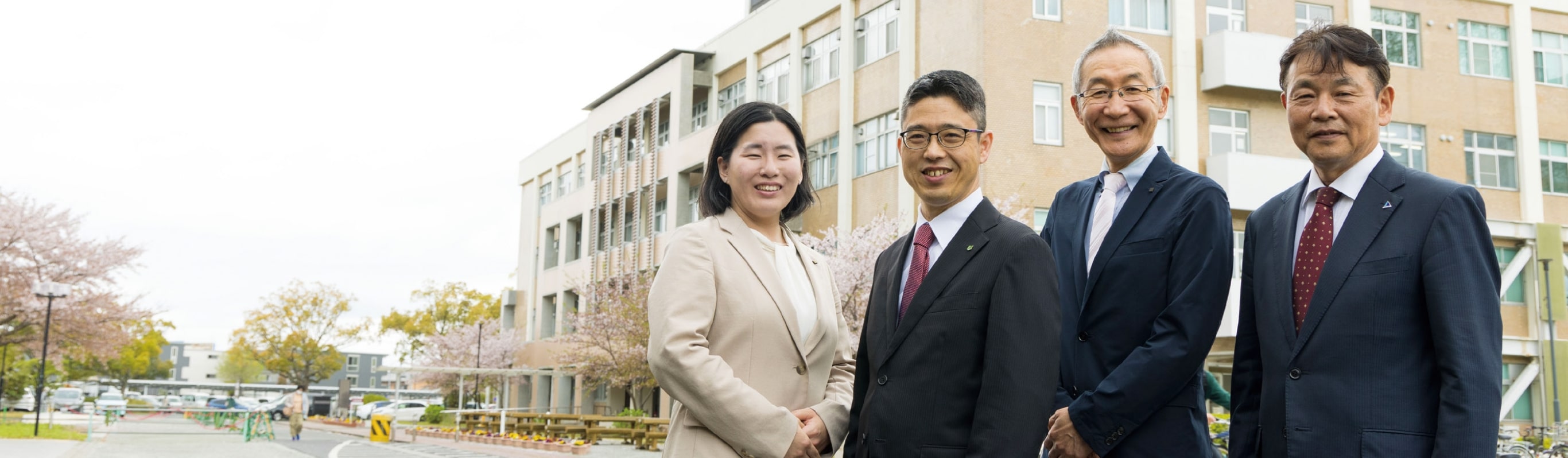
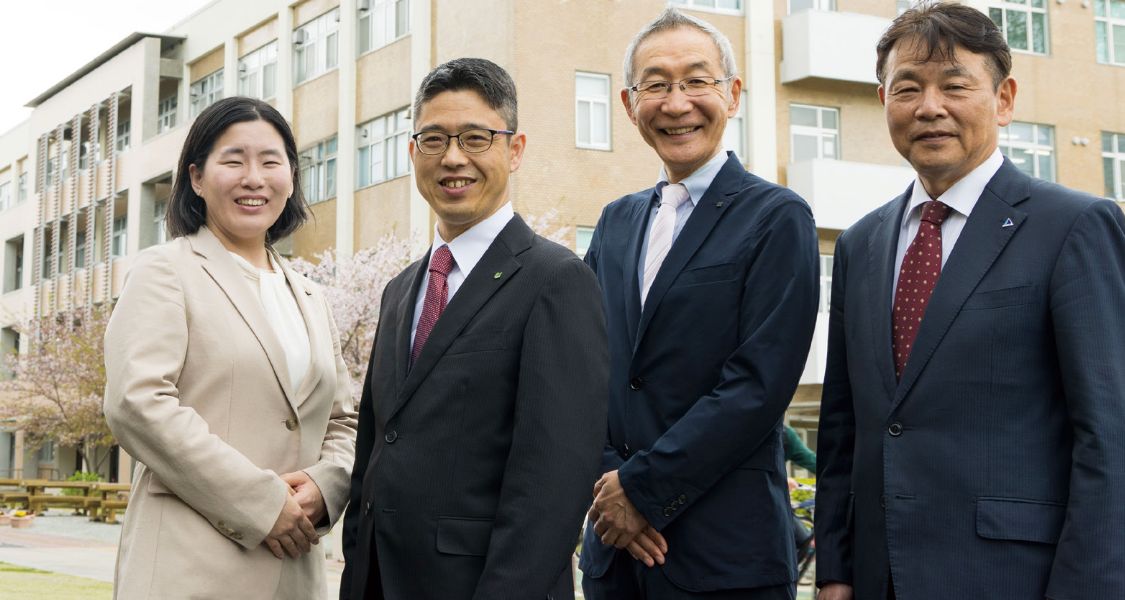
A challenge to circular economy that began with “awareness” and “encounter”
- Making furniture from coffee bean grounds -
At ITOKI, we pursue the possibilities of new materials that have never existed before in the world, and promote research in our technology development organization.
As part of this effort, we are implementing an initiative to upcycle furniture material by using coffee bean grounds, which have previously attracted attention for their deodorizing and deodorizing effects and have been explored for various ways to use them.
This time, two of us spoke with Professor Nonaka of Mie University, a leading expert in wood biomass research who was involved in the project, and Executive Officer Asai of Dalton, a group company, about the current state of research and future possibilities. I did it.
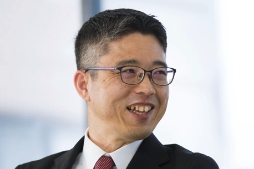
Ph.D. (Engineering). Specializes in biomass science (chemical engineering, agricultural chemistry, wood chemistry). Since his graduation research, he has been engaged in various biomass research for over 25 years. After arriving at Mie University in 2005, he focused on wood materials such as wood, aiming to implement wood biomass in society and contribute to decarbonization.
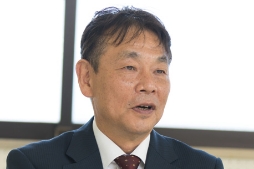
Since joining the company in 1990, he has been engaged in engineering and development work, working to improve the performance of powder machinery and powder technology. Obtained a degree from Osaka Prefecture University (at that time) in 2017. Doctor of engineering.
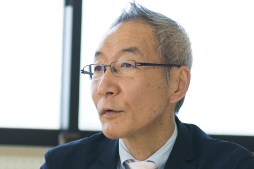
Joined Itoki in 2007. Since 2010, he has been involved in product development as a founding member of Econifa, a solution for utilizing domestic materials. After transferring to the Product Development Division, he continued to develop solid wood products, and last year began researching bio-based materials in a concurrent position.
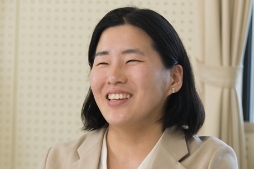
After completing a master's degree in mechanical engineering, he joined Itoki. Started developing and designing chairs, stools, etc. In 2022, a department specializing in materials will be established within ITOKI and will begin considering furniture made from coffee bean grounds.
New materials research undertaken by Mie University x DALTON x ITOKI
Initiatives to utilize wood-related resources
―Until we reach the coffee bean dregs―
- small island
-
Recently, the term circular economy has been heard in many places. As a word related to this, there is a coined word in Itoki called ``Econifa''. This word is a combination of the words "eco" and "coniferous" and refers to the solution we started in 2010, specifically by harvesting Japanese wood, cedar, cypress, and other trees that are ready for felling. , refers to efforts to utilize it for office furniture and public facilities. At that time, plastic-free and carbon-free activities did not receive as much attention as they do now, and the term SDGs did not exist. Although the actual initiative was relatively small-scale, we believe it was of great significance in that it focused on making more effective use of Japan's forests, which make up about 70% of the country.
- Nonaka
-
My laboratory at Mie University is called the Wood Molecular Materials Control Laboratory. Wood includes not only wood, but also bamboo, rice straw, etc., and our theme is how to effectively utilize these materials. A distinctive feature of our research dealing with wood is that we aim to utilize all the components contained in wood materials. In particular, we have focused on the use of the three major components of cellulose, hemicellulose, and lignin, and have continued research into extracting and using these components.
Meanwhile, around 2016, we began research into ways to not only take the time and effort to extract the ingredients, but also create products using the powder obtained by pulverizing the material. Since we use powder, we use all the ingredients. Initially, wood flour and paper flour were used as raw materials, but the scope has since expanded to include the use of various materials such as coffee bean grounds and bamboo flour.
Two people with the same aspirations come together
―Mie University and Itoki, the impetus for collaboration―
- Nonaka
-
Research on coffee bean grounds in the laboratory began when a student working part-time at a convenience store noticed that a large amount of the coffee bean grounds produced during drip coffee was being discarded. I later learned that 600,000 tons of coffee bean dregs are produced each year. When I started my research, I didn't think much of soybean waste disposal, but it turned out to be a major social issue.
- small island
-
We started this research because the director of the Materials Research Institute at the time told us, ``We want to think about recycling various materials.As a starting point, we want to do something with coffee bean dregs, which is a familiar item.'' I started doing research while concurrently working in product planning.
When I first started my research, I had a relatively simple idea that coffee bean cakes are powder and could be used for furniture as soon as they were ground, but when I actually tried it, I realized that just drying the discarded bean cakes was enough. It was difficult.
At an impasse, we desperately called Associate Professor Adachi of the Advanced Wood Processing Research Institute at Akita Prefectural University, who had collaborated with us on the product development of Econifa and had given us scientific advice about wood. I did. There, I was introduced to Professor Nonaka.
Drying, molding, and solving various problems to commercialize products
-How coffee bean grounds become office furniture-
- Nonaka
-
To explain the division of roles in this research, Dalton, where Mr. Asai works, collects the coffee bean grounds and grinds them finely. After that, Mie University mixed the materials, molded them, and then used ITOKI to make furniture.
- Asai
-
One of the challenges faced by Dalton in the grinding process was drying. Dryness is a prerequisite because if the material is not dry when grinding, it will stick inside the equipment and will not work efficiently. The coffee bean grounds that we actually obtained were still in the shape of a dripped cone, about 5 cm long, and because they were too large, they did not dry easily, and the material was wet, so we used a general crusher (loosener). ), so much adhesion occurred inside the equipment that it could no longer be operated continuously. The big question was what to do about this.
This is where our granulator came in handy. A granulator is a mechanism that molds wet powder by adding liquid to the normally dry powder to moisten it and create granules. If it's okay to wet something dry, then it might be possible to use it on coffee bean grounds that are already wet, so I tried running coffee bean grounds through a granulator. After converting large conical blocks into small particles with a diameter of about 8 mm, drying and crushing became more successful. I was a little worried about whether the powder after grinding would have the particle size that Professor Nonaka had requested, but I remember being relieved when he approved the measurement results. - Nonaka
-
While working on the project with Itoki, I was honestly surprised when I learned that Dalton was an Itoki group company. In our laboratory, we use Dalton mixers and a large number of Dalton-made draft chambers and laboratory benches. For this project, deciding on the crushing process was a big issue, and having Mr. Dalton on board was extremely reliable.
Once the fine powder of coffee bean lees is produced, the next step, which my laboratory is in charge of, is kneading, which involves mixing materials that act like glue to connect the powders together, and forming the powder into a plate shape. For plate molding, we are using a molding machine designed for ceramics, as we believe that extrusion molding technology, which molds ceramics and clay to make things like rods and roof tiles, can be applied. This time, with commercial use in mind, Mr. Itoki was present as the work progressed using a relatively large molding machine.Actually, as long as you have coffee powder, it is relatively easy to extrude it into a shape, but the difficult point is whether the dried plate will have a nice shape after that. Small sizes may work well, but larger sizes often cause problems such as warping when drying. Solving these problems is where we can show off our skills.
- Sakata
-
For this project, Itoki was responsible for the actual furniture production, and created a stool as the first prototype. As Mr. Nonaka pointed out, the actual material we made warped, so it was extremely difficult to eliminate this warping. It was quite difficult to search for the most optimal pressing method while trying various press conditions to eliminate warping of the plate-shaped material. In the end, I was able to overcome this problem and was very happy when the prototype was completed.
Looking at the prototype that was completed thanks to the efforts of Dr. Nonaka and Mr. Dalton, coffee bean grounds have great potential to become a good material. Therefore, ITOKI feels that it has a great responsibility to create products that customers can actually use.
The future expands towards establishing a circular economy
-The challenge of all-biomass materials-
- Nonaka
-
Our initiative is being carried out as an industry-academia collaborative activity related to a research project* by the Ministry of the Environment, and we have just completed the first year of the three-year project. Our laboratory's mission in this project is to establish a technology that can mass-produce materials that have both dimensional control and water resistance using coffee bean grounds. Once the technology is established, I believe that companies will actively develop products using the material, which will meet my goal of social implementation. I think it can be said that we are currently taking a steady step towards that goal.
- FY2020 Environmental Research Promotion Fund “Establishment of biomass powder extrusion molding/water-resistant system using cellulose derivatives as auxiliary agent” (Research representative: Hiroshi Nonaka)
- Asai
-
At Dalton, we believe that we have been able to meet requests regarding the establishment of grinding technology related to the use of coffee bean grounds. In the future, we plan to tackle the issue of how to achieve stable production efficiently and in a manner that minimizes energy use. In order to establish a circular economy for coffee bean meal, we would like to work on establishing a method that can produce it stably and cheaply.
- small island
-
I think of ITOKI's goals from two perspectives: short-term and medium- to long-term. In the short term, we believe it is important to use materials that can be made with current technology to develop attractive products that customers will be happy to purchase and use.
From a longer-term perspective, we need to change our way of thinking and stance towards Itoki's materials. Some of our products still rely on adhesives and paints derived from fossil fuels, so in the long term, we would like to work on developing new materials and products that are free from fossil fuels, not just coffee bean grounds. I am. - Sakata
-
I was involved in the communication between companies to turn materials made from coffee grounds under Kojima into actual furniture, and the arrangement of stools in a block style. Personally, in order to realize ITOKI's vision, I would like to stick to steady efforts to stay close to our customers and identify their needs.
- Nonaka
-
Mie University, Itoki, and Dalton have each set their own goals, but from a broader perspective that goes beyond the three parties' positions, I think this project can be summarized as a challenge to create all-biomass materials.
Trends in materials research around the world are moving toward switching to all-biomass materials that do not use petroleum-derived raw materials, such as replacing plastic straws with paper straws, and even replacing previously unthinkable items with biomass materials. There is a growing movement to do so. Methodologically, we can replace petroleum-based plastic materials with bioplastics, wood or paper products, separate wood components and use them as my laboratory has done, and solidify wood powder. Various methods, such as ways to create alternatives to plastic, are all based on the basic idea of changing materials to plant-based ones.
Our current efforts are the challenge of creating all-biomass materials, but we believe that we can see a path ahead that will lead to the establishment of a circular economy.
“Coffee Grounds board” will be exhibited as a reference at “EcoPro 2022”
In connection with the joint research theme of this time, the use of coffee bean grounds, we produced a board called "Coffee Groundsboard" that can be used as a material for furniture and other materials. We held a reference exhibit at the environment-related exhibition "EcoPro 2022." Until now, attention has been focused on coffee bean grounds for their deodorizing and deodorizing effects, and various ways of using them have been explored, but this time, an upcycling initiative to use them for furniture attracted the attention of the venue. .